Prior to the early 1970s, many hydraulic elevators were installed with buried (in-ground) hydraulic jack units with a single flat plate lower bulkhead. This design was in accordance with the elevator code at the time. Many of these jack units were buried in the ground without any corrosion protection at all. Soil conditions vary throughout the country with some conditions harsher than others. Anytime an unprotected metal cylinder comes in contact with the soil, electrolysis and/or corrosion will occur to varying degrees (depending on location).
Failures on these older design jack units due to electrolysis and/or corrosion, particularly at the lower end where the flat plate is welded to the cylinder, have caused rupturing of the cylinder and uncontrolled descent of the elevator. Because of these possible failures, the elevator code was revised in the early 1970s and required that all in-ground jack units be provided with a safety bulkhead and a dished (concave to pressure) bottom head. A flat "safety" bulkhead is welded inside the cylinder at the lower end and the dished bulkhead is welded below the flat bulkhead to close the cylinder. The inner flat bulkhead includes a small hole to allow the controlled descent of the elevator (15 fpm max. per code) should the dished bulkhead fail.
The new ASME A17.1-2000, Scope - Part 8, and Section 8.6.5.8 contains provisions that all in-ground jack units include a safety bulkhead and dished head. This new code is being adopted by an increasing number of state and local governments and is requiring that all "flat" bottom jacks of obsolete design be replaced by new "dual bulkhead" jack units. Elevator Equipment Corporation (EECO) strongly
recommends that all owners of buildings that include elevators with the old "flat" bottom design jack units replace the cylinders or jack units as soon as possible, regardless of whether their local enforcing authorities have adopted ASME A17.1-2000 or not. EECO also recommends the installation of sealed PVC around the replacement cylinder to comply with Section 3.18.3.8 of the new code.
Inspection and maintenance is an important part of hydraulic elevator ownership. Since visual inspection of in-ground piping is not possible, it is essential that in-ground cylinders and piping be examined and tested on a regular and frequent basis. While EECO does not install or maintain elevators, we strongly recommend strict adherence to an on-going maintenance and inspection program, as is spelled out by ASME A17.1 code for elevators, Sections: 8.6.1.2 through 8.6.1.4, 8.6.5.5, 8.6.5.7 and 8.11.3.2.
It is especially important to check and monitor oil levels regularly to detect possible oil leaks. Frequent re-leveling, tripping of low oil timer, difficulty or laboring of the car to reach its highest landing, are indicators of a low oil condition and possible leak. If loss of oil is suspected and cannot be corrected above ground, then indications point to an in-ground leak.
At the first signs of a leak, the unit should be immediately taken out of service. Do not add oil to the system without determining the source of the oil leak and correcting it. A full load pressure test of the complete hydraulic system should be performed. This includes testing the cylinder, piping and the pressure relief valve.
Proper maintenance and system pressure testing are the most effective methods to detect possible leaks. Properly maintained systems with code compliant double bottom cylinders with sealed PVC liner provide maximum protection from the risks to passenger safety and environment.
EECO specializes in cylinder and jack unit replacement. We offer owners of older "flat" bottom jack units an exact replacement cylinder or a complete jack unit, regardless of original manufacturer. EECO can also provide a complete sealed PVC liner as well as a sealed PVC leak monitoring system for your replacement jack unit.
EECO has two manufacturing facilities to serve our customers from coast to coast. One facility is located in Los Angeles, California and the other is in Richmond, Indiana. All EECO products are manufactured in strict accordance with the Safety Code For Elevators & Escalators, ASME A17.1. Each phase of the manufacturing process is monitored and checked to assure that each jack unit component is built and assembled in accordance with engineering and shop order specifications.
ASME A17.1-2000
Safety Code For Elevators & Escalators
SCOPE
Part 8 contains general requirements for new and existing equipment.
NOTE: Requirements 8.1, 8.6, 8.7, 8.9, 8.10 and 8.11 apply to both new and existing installations.
3.18.3.4 Safety Bulkhead. Cylinders buried in the ground shall be provided with a safety bulkhead having an orifice of a size that would permit the car to descend at a speed not greater than 0.075 m/s (15 f/min), nor less than 0.025 m/s (5 ft/min). A space of not less than 25 mm (1 in.) shall be left between the welds of the safety bulkhead and the cylinder head. Safety bulkheads shall conform to 3.18.3.6.
A safety bulkhead shall not be required where a double cylinder is used and where both inner and outer cylinders conform to 3.18.3.6.
8.6.5.8 Safety Bulkhead. Hydraulic cylinders installed below ground shall conform to 3.18.3.4 or the car shall be provided with safeties conforming to 3.17.1 and guide rails, guide rail supports, and fastenings conforming to 3.23.1.
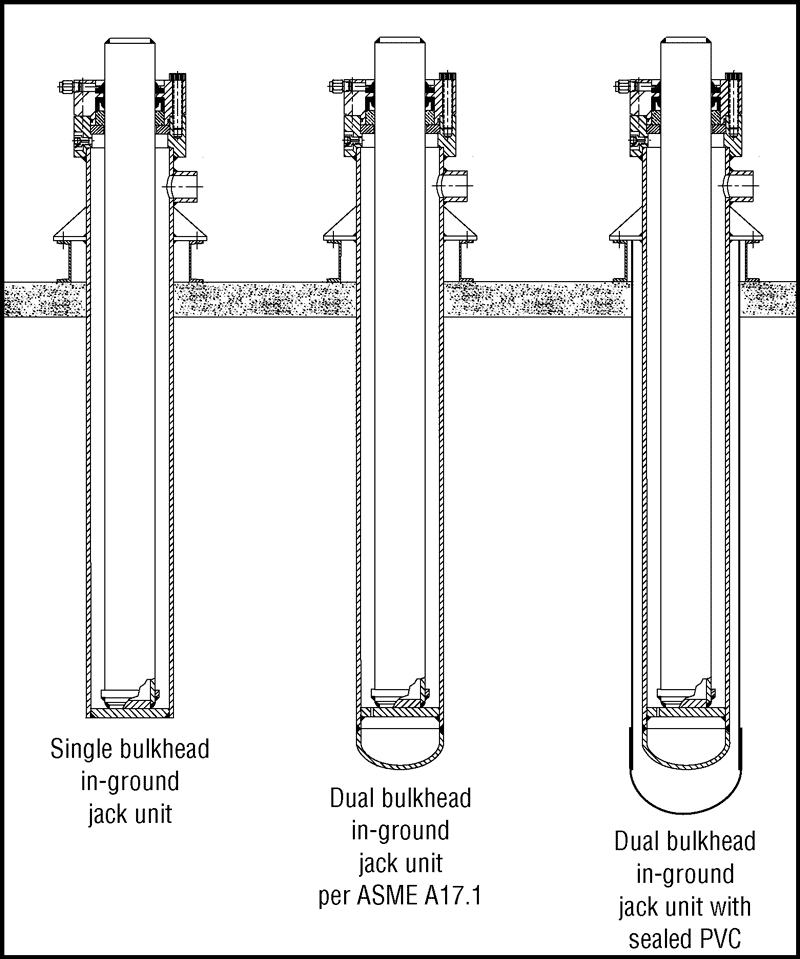
Whether you need to replace a cylinder or a complete jack unit, Elevator Equipment Corporation can quickly provide a solution. Contact EECO sales to request a quote/order form or you can fill it out or download it from the EECO website Here.